廃棄インキ缶ゼロを達成〜残肉削減で環境負荷低減にも貢献
KGK・自動UVインキ供給システム導入
(株)光陽社(本社/東京都文京区、犬養岬太社長)は、同社の生産拠点である飯能プリンティングセンターBASE(埼玉県飯能市)において、ケイ・ジー・ケイ(株)の自動UVインキ供給システム「Fine Side 200」を導入し、廃インキ缶の完全排除やインキ残肉の削減など、産業廃棄物の大幅削減とインキ供給作業がない効率的な運用を実現している。今回、同社・生産本部システム部 部長の千葉達也氏と専門課長代理の菅波聡一郎氏にパイピングシステムを導入した狙いや導入後の成果などについて聞いた。
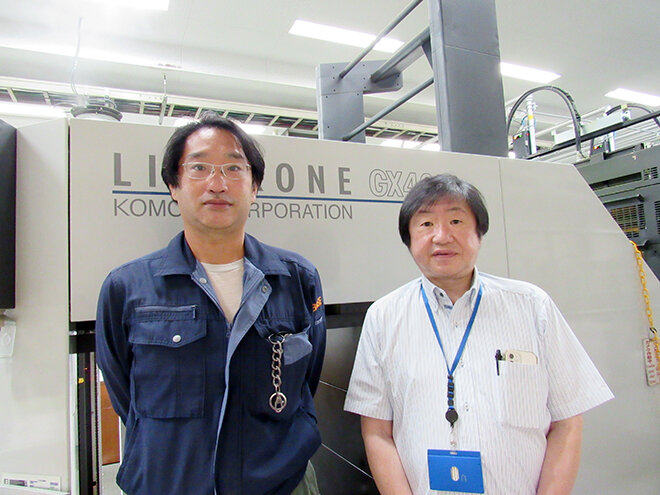
同社の生産拠点である飯能プリンティングセンターBASEは、太陽光発電装置の設置やグリーン電力を採用するなど、生産活動において発生する温室効果ガスの削減に努めており、現在ではScope1とScope2におけるCO2排出量が実質ゼロで稼働する、カーボンゼロプリント工場となっている。同工場で印刷する製品は、すべてカーボンゼロプリントとして提供することが可能であり、顧客のSDGsへの取り組み、ESG経営に対し、「印刷」で貢献している。
その取り組みは、業界内でも高く評価されており、2021年には、(一社)日本印刷産業連合会が印刷産業界における各企業の環境問題に対する取り組みを促進するとともに、印刷工場の環境改善および印刷企業に対する社会の一層の支持・理解を獲得することを目的に実施している「第19回印刷産業環境優良工場表彰」において、「経済産業省商務情報政策局長賞」を受賞している。
オペレータの作業負荷低減に効果
その同社が自動UVインキ供給システム「Fine Side 200(以下、パイピングシステム)」を採用したのは2019年のこと。同社としては、2台目となるKOMORI製のH-UV8色両面印刷機の増設に合わせて導入している。H-UV8色両面印刷機は、ワンパス両面印刷という高い生産性を誇る一方で、高生産性であるがゆえにインキ供給作業も増えていく。インキ供給作業は、そのたびにオペレータの負担となり、トータル的な生産性にも影響を及ぼすこととなっていく。この作業負荷の削減と高効率生産の実現が導入した狙いの1つだ。
2台の8色両面機でパイピングシステムを採用
この増設にあわせ、既設のH-UV8色両面印刷機ともパイピングシステムをつなぎ、2台のH-UV8色両面印刷機のインキ供給の自動化を構築している。
同社が導入したパイピングシステムは、多種多様なUVインキの大容量供給に適応するため、UVインキ接液摺動を行うポンプ・制御弁の主要部品に独自の硬化抑止技術を採用。油性インキに比べて流動性が低いUVインキの部品固着や硬化生成物による異常摩耗を抑えて高耐久化している。UVインキ圧送不具合の回避のために、ポンプへの負荷を軽くする目的でこれまで制限されてきたインキパイピング長さを大きく延ばせるようになるため、インキ供給設備・パイピングのレイアウト自由度を広げることが可能。同社が導入した200kgドラム缶用新型ポンプの最大吐出量は毎分900ccで、新型分配制御弁と組み合わせることで1台のポンプから最大毎分200cc×4胴へのインキ同時補給を安定的に行うことができる。
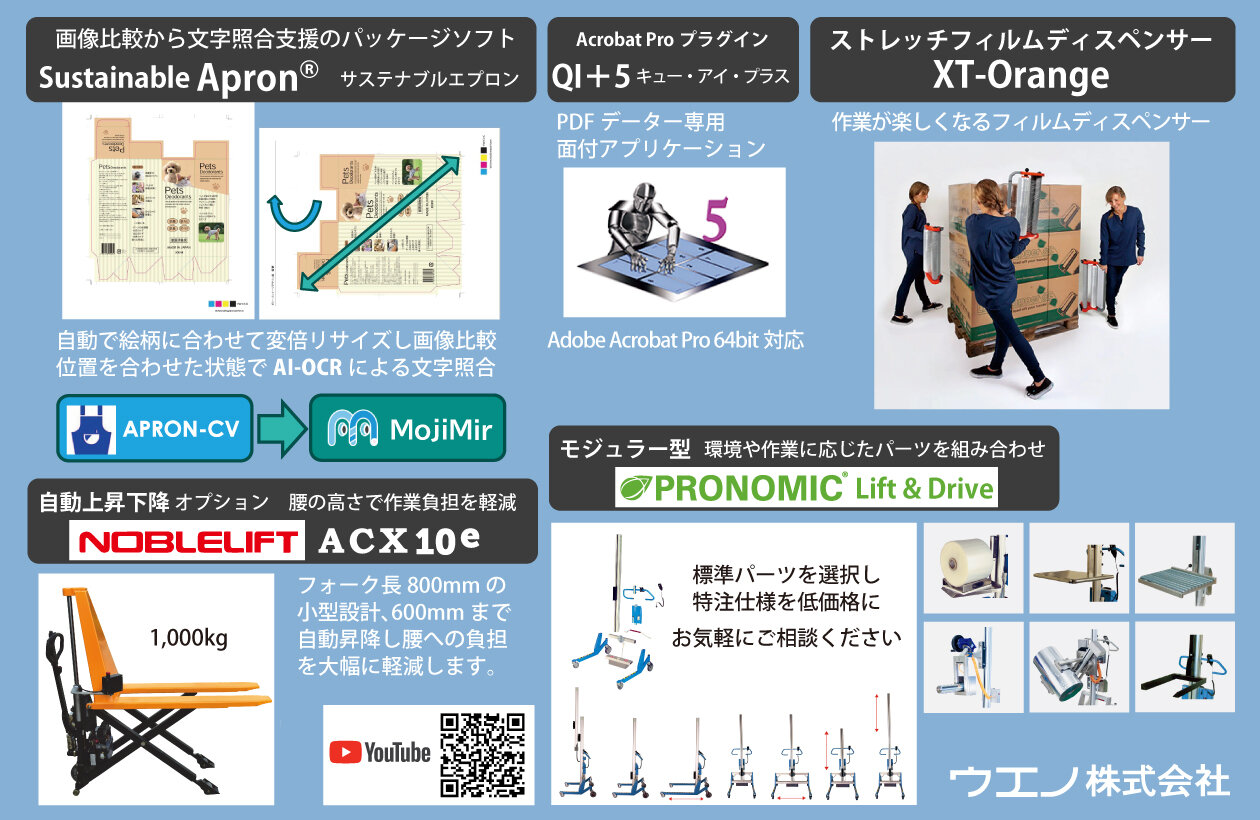